Problems: The customer produces machined parts for the automotive industry. They were using a hand-loaded gravity track for grinding operations. This led to inconsistency in the way parts were loaded, which caused stops and starts to the process. Also, parts were infrequently damaged from rough handling in this loading process. They sought an automated solution to the downtime caused by hand loaded parts and a way to eliminate damage to the parts.
Solutions: Fortville Feeders built a bowl feeder system that automates the loading process with a pneumatic gripper and servo controlled programmable pick and place. This allows one operator to attend multiple grinders without hand loading any of them. This eliminated the inconsistency in loading. The feeder system consists of a bowl feeder with a hopper, a track system that feeds parts to a dead nest. The gripper then consistently loads the parts on the grinder in-feed track. The system loads parts at the rate of 13 ppm.
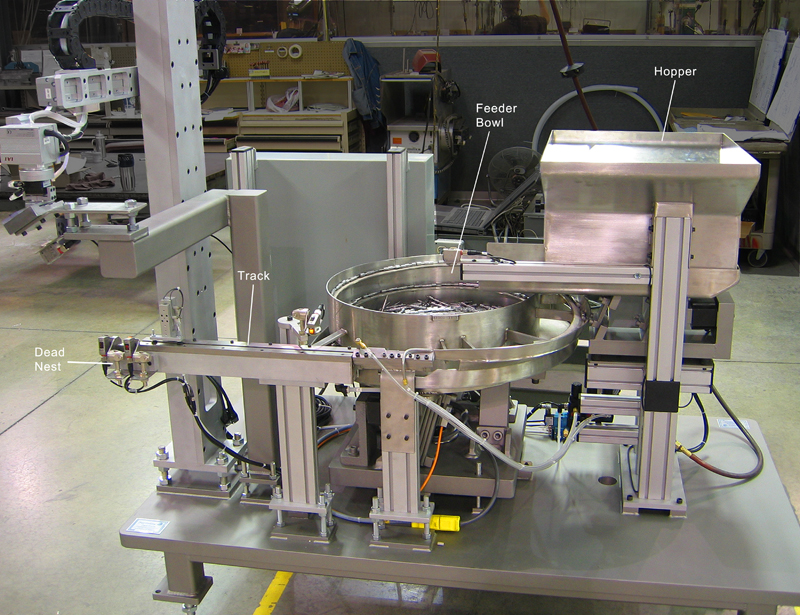
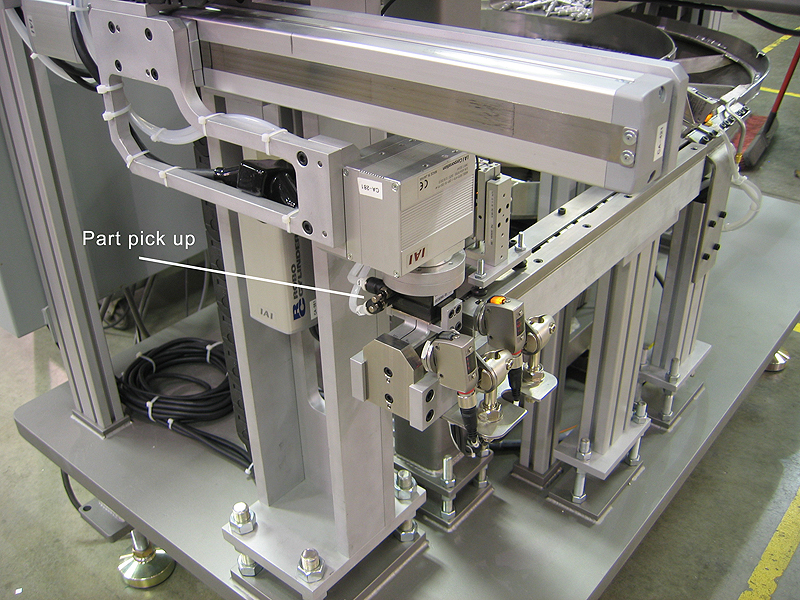
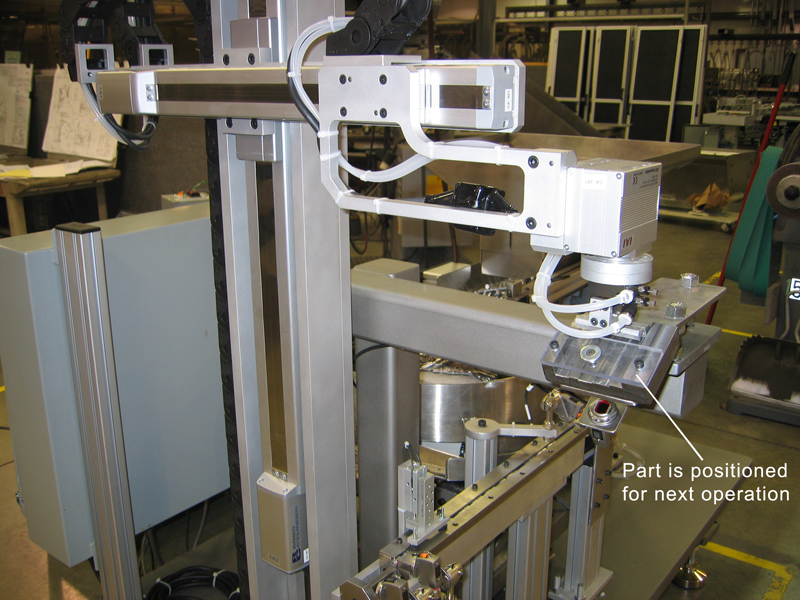
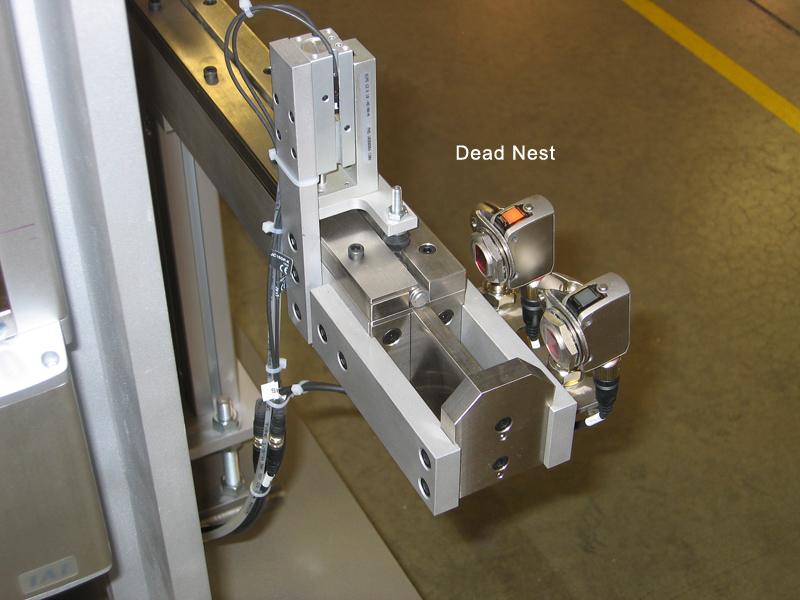
Recent Comments